Directional Composites through Manufacturing Innovation (DiCoMI)
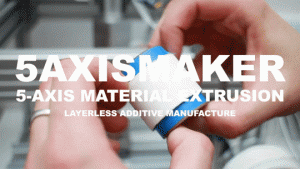
DiCoMi project aims to bring together leading innovators from 11 countries, across Europe, and beyond, to develop a new method of producing composite material parts with optimised fibre directionality. The DiCoMI project will integrate advanced manufacturing techniques, composite materials science, and manufacturing system design. As such, it requires a high level of inter-disciplinary cooperation as well as collaboration between researchers and industrials. The outcome will be a truly novel composites manufacturing system capable of producing parts with increased accuracy, reduced cost and enhanced functionality.
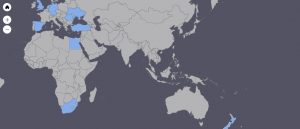
DiCoMI project will focus on Directional Fibre-Reinforced Polymers (FRP) materials and combined different manufacturing techniques into a unique and innovative hybrid system. DiCoMI project will have a direct impact on the European and international scientific state of the art in the fields of composite materials and manufacturing equipment, while supporting the innovation
potential in the automotive and aerospace industries.
In this project, Sabanci University will collaborate with KordSA as Turkish partner. The total project budget is €1.42M of which €157K and €90K are allocated to Sabanci University and KordSA, respectively. The project is planned to start in 2018-March for 48 months.
The project is supported by EC under H2020-Marie Skłodowska-Curie Research and Innovation Staff Exchange programme.
Status: Started as of March 2018
Development of Position and Orientation Tracking System and Vibration Suppression System for Robotic Machining
Industrial robots were initially designed for part transfer, welding and automation. Recently, they have started to be used for machining applications of large scale parts. However, due to their structural and control system design there have been several issues faced with regards to due their applications in machining. The major problems are excessive inaccuricies in tool path contouring and low frequency vibrations in metal cutting. In this project, it is aimed to develop sub-systems for industrial robots to increase their effectiveness towards robotic machining applications which are very suitable in manufacturing of parts for aeronautical, naval and automotive industries, by increased toolpath contouring accuracy and suppressed low frequency modes.
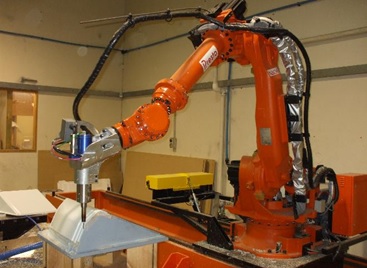
The 36 months project will be led by Asst. Prof. Dr. Lutfi Taner TUNC, who is working as faculty member of Sabanci University, Faculty of Engineering and Natural Sciences. The R&D activities will be carried out cooperation with Modesis Makine Elektronik ve Bilişim Teknolojileri Co. In Image processing appllications, Prof. Dr. Mustafa ÜNEL from Sabanci University Faculty of Engineering and Natural Sciences will consult to the project. R&D consultancy from Dr. Jokin Munoa who is the group leader of vibration control at IK4-IDEKO, will be gathered in the vibration suppresion area. The compatibility of the applications to the industry will be checked and sustained by getting consultancy and technical support from industrial parties. Sabanci University will support the project by funding 3 PhD and 1 MSc Student. The project consortium members are complement each other in order to achieve the project targets.
This project is supported under TUBITAK-1003-Primary Subjects R&D Funding Programme-2017/1 Calls.
The proposed budget of the project is TRY-1.8M
Status: Started as of 15th May 2018
Process Modelling and Process Development Techniques for 5-axis Abrasive Water Jet Cutting Processes
Abrasive water jet (AWJ) cutting processes can be used to machine materials such as nickel and titanium alloys that are difficult to cut with conventional milling due to very low tool life. However, it is mostly used in the production of profile geometries for the purpose of 2-axis circumferential cutting where the part is thoroughly cut. The erosion rate, hence the kerf width and depth, in AWJ depend on the pump pressure, abrasive rate, jet impact angle and the feed rate. If the cutting depth to which the water jet can act can be simulated in advance, more efficient process conditions can be achieved and it can be used in 5 axis jet milling type of use rather than only 2 axis cutting.
AWJ processes provide significant advantages in cutting of hard materials, however, the knowledge of this area is limited. Due to the relatively new processes, there is a need for knowledge in process modeling, application and parameter selection. In this project, the theoretical modeling of 5-axis abrasive water jet processes and experimental and theoretical analysis will be studied. Modeling of the abrasion space (“kerf”) of 5-axis abrasive processes, the effect of abrasive process parameters on the process performance and the simulation of the part surface will be studied. In addition, compensation of dimensional errors caused by the process be applied on 5-axis toolpaths through compensation methods. The developed model will be experimentally verified and, if necessary, corrected on the model. The project will also include the application of the 5-axis abrasive cutting process to the industry and analyze the economic and usefulness of this manufacturing process. Parts selected from different sectors and which may be potentially advantageous for abrasive waterjet cutting processes will be selected and efficient processing conditions will be determined for these processes using process models developed in the project. Project outputs and application results on parts will be shared with related industrial organizations. The field of development of the project will be an important contributor to the necessary knowledge and scientific infrastructure both in academic and industrial aspects.
R&D consultancy from Dr. Matej Sulitka who is the group leader of process simulation at RCMT-CZECH TECHNICAL UNIVERSITY IN PRAGUE, will be gathered in representation of 3D workpiece geometry. The compatibility of the applications to the industry will be checked and sustained by getting consultancy and technical support from industrial parties. Sabanci University will support the project by funding 1 PhD and 1 MSc Students.
This project is supported under TUBITAK-1001-Scientific and Technological Research Programme-2017/2 Calls.
The proposed budget of the project is TRY-180K
Status: Started as of 15th May 2018